
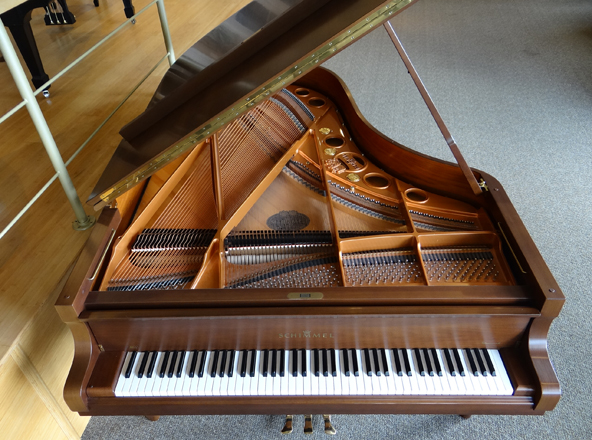
This concept is not mere indulgence in luxury, but a solid basis for the construction of premium quality instruments.
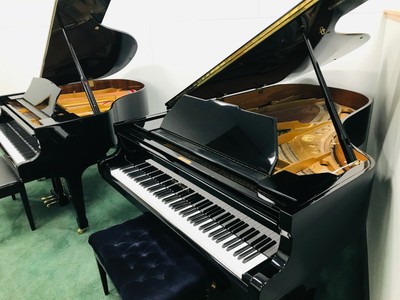
It could equally be asked whether is it absolutely necessary for the hammer-head felts to be manufactured from the wool of specially reared merino sheep? Yes, without doubt, as it is top-class materials which provide the prerequisites for a first-class sound. Some might consider it a quirk to utilize up to 300 year-old mountain spruce from premium mountainous areas for Schimmel soundboards: Schimmel’s masters call it quality. Craftsmanship at Schimmel represents a capital investment which has grown over more than a century and is fostered new every day! The stuff of which music is created It takes three and a half years to complete the training as a specialist piano manufacturer, and a further nine and a half years are necessary to achieve the title of master Schimmel is one of few the manufacturing firms to offer this opportunity. Some of Schimmel’s manufacturing specialists currently employed have fathers – or in some cases even grandfathers – who were also employed within the same profession.

Additional necessary attributes include comprehensive knowledge and skills relating to the casing, a love of the natural produce wood and the artistic design of individual inlay work.Įxperience in these areas has been cultivated, preserved and passed on for several generations in the firm. The same applies to the over 10,000 individual elements of each instrument which must all be meticulously synchronized with exact precision: from the fitting of the strings, the positioning of the hammer-heads and the regulation of the action, to the fine art of tuning and voicing. This specialized task requires a highly sensitive and well-trained ear, which cannot be substituted by an electronic instrument. For example, the voicing of the instrumental timbre is formed by extensive needling – several hundred times per hammer-head – a total of 88 per instrument. The quality of each individual instrument is dependent on this specialized craftsmanship. To achieve a consummate tone, specialists are required with instincts who have a feel for the most minute tonal nuances, and also possess a high degree of patience. Both upright and grand pianos are extremely sensitive instruments. The piano craftsmen at Schimmel employ their entire range of experience and commitment to enable pianos and grand pianos to develop their natural tonal volume, allow great compositions to be performed with appropriate tonal strength and permit pianists to display their virtuosity. The family firm continued to flourish: by the end of the 1950s, Schimmel instruments were the most frequently purchased pianos in Germany – and were being sent all around the world. In 1927, his son Wilhelm Arno Schimmel took over the management of the company and relocated the site to Braunschweig (Brunswick), where he developed one of the major innovations of the 1930s: a small piano without back posts, with a newly designed action and a unique tonal character. Both he and his slogan, “Quality will prevail,” were proved right by his success. His instruments were impressive for their advanced technique, excellent tone and contemporary form. Shortly after the completion of his training as a piano manufacturer, he established his own workshop in Leipzig and produced his first piano at the beginning of 1885. Both of these qualities were demonstrated by Willhelm Schimmel, the founder of the company. Since 1885, it has been Schimmel’s passion to employ artistic craftsmanship, and knowledge to enable uncounted people, famous, well-known and unknown, to achieve their keys to happiness. Each note a concert experience Four generations – One passion
